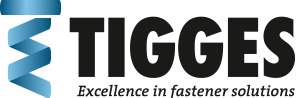
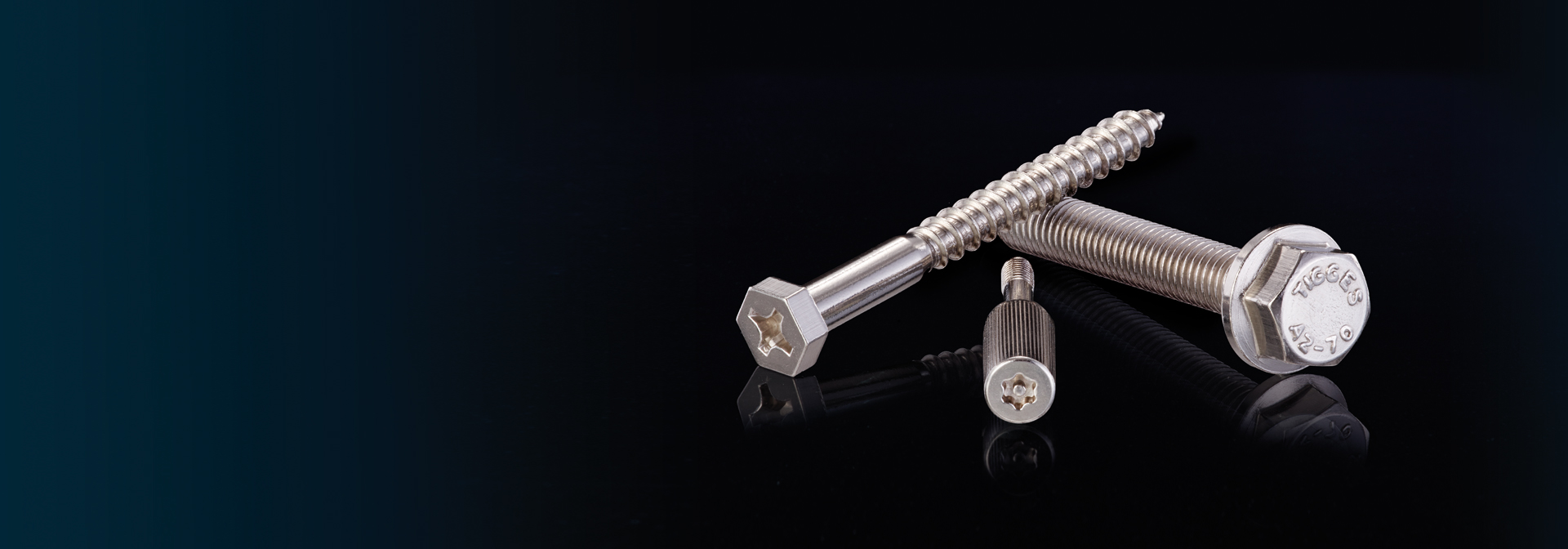
German
"Wertarbeit"
Extensive quality
The German term "Wertarbeit" describes a product that delivers what it promises. As a company with German roots, we are committed to this claim and achieve it through consistent quality management. As a supplier to many industries, including the automotive, electronics and energy sectors, we meet stringent global standards by providing measurable product and process data.
But for us, the concept of quality is much more than this. It also means service, commitment, innovative capacity and solution orientation – all important criteria that are ingrained in our corporate culture. All this means that you can be assured of the vital element that you are looking for in a C-parts supplier: reliability.
Incoming quality inspection
Our incoming goods inspection checks the material before it enters the production process. But this is not the first step in our quality assurance. Our supplier management has already defined our suppliers' manufacturing processes. So the concept of quality is already part of the value chain before it reaches our production.
Process monitoring through SPC
We use SPC to monitor the process capability of our production and ensure its long-term operation. This statistical process monitoring does not focus on the precision of the component that is tested, but rather on the production process itself, which is continually evaluated using statistical methods.
Process inspection
Process inspection is the key to consistent quality, especially over higher volume of production lots. With strict in-process inspection of each manufacturing process in place, we can ensure that parts are supplied to our customers with consistently good quality so that our customers have the peace of mind to use our parts without having to worry about parts that may be out of spec and eventually interrupt their assembly process.
By applying the latest measuring equipment, such as optical inspection, we can take and inspect multiple measurements with the push of a button not only to produce parts within the specifications and tolerances, but also to produce parts which require a certain CPK value (Process capability Index) which is monitored and recorded for each manufacturing process.
Final inspection
In addition to our tight in-process inspection, no product leaves us without being inspected and recorded again against all required measurements, tolerances, mechanical properties and even appearance requirements to ensure our customers receive parts which match the specifications.
By having our own laboratory, we are able to use any measuring technique, from projector, contractor, hardness and tensile tests to automated optical inspection.
Each product is produced with individual inspection plans specifying not only all tolerances, mechanical properties and appearance requirements, but also the type of testing to be carried out before being approved and delivered to our customers.
PPAP IATF 16949
As an IATF 16949 certified company, we offer a professional production part approval process (PPAP) for the approval of serial parts. For the product and process approval, we provide the required measurement, material and function reports on standard forms (also paperless) and ensure an efficient exchange in the release process.
100% optical inspection
In many cases and in today's automated assembly lines 100% inspection has become a norm to ensure parts are supplied close to “zero ppm”. To achieve this, state-of-the-art, automatic inspection machines are required.
With a variety of optical inspection machines and even eddy current machines to inspect internal cracks and hardness, we can provide parts which are inspected 100%. Our machines will inspect every single part with a throughput of up to 500 pcs/minute to allow high-volume inspection.
Precision up to µ
To ensure dimensional accuracy, we use the latest methods of measurement, including a Mitutoyo Contracer for high-precision contour measurement, camera systems and digital projectors which examine up to 500 components per minute with an accuracy of up to 20 μ. In this way, we ensure the necessary product quality, which in turn ensures uninterrupted production for our customers' assembly lines.
Lasting quality
Our experience with materials and our expertise in surface treatments means we produce fasteners that provide a perfect balance of application, durability and economy. A test laboratory with chemical and physical testing equipment is available for this, including a salt spray system that provides information on corrosion resistance and gives us a significant competitive edge in the offshore industry.
Certified quality
Our quality management is certified according to ISO 9001 and IATF 16949. In addition, we meet and exceed many industry and company standards.